Once a wind farm has been set up, a test phase and connection to the transmission grid follows. Then the actual operation of the wind farm begins.
The control of the individual areas - safety, maintenance, repairs and operation is called technical management and the control of the economic processes is called commercial management.
After planning and construction, the correct operational management is decisive for optimising a wind farm investment - by acting with foresight, plant availability can be increased significantly.
Some corporations that own wind farms do not intend to monitor the operation of their wind farm themselves. In this case, in contrast to traditional power plants, the operation and maintenance of a wind farm is often outsourced to suitable specialists. The scope of tasks is tailored to the needs of the wind farm owner.
With over 20 years of experience, the Max Renewables team can ensure the optimisation of the operational management.
**
Economical operation and maintenance
The primary objective of operations management is to reduce the generation costs per megawatt hour of electricity to a minimum over the lifetime of the plant. This can be achieved by the following strategies:
- The minimization of operating, maintenance and repair costs
- The increase of the energy yield and increase of the economic yield by optimizing the sales price
- The reduction of the insurance risk
- The protection of the installations
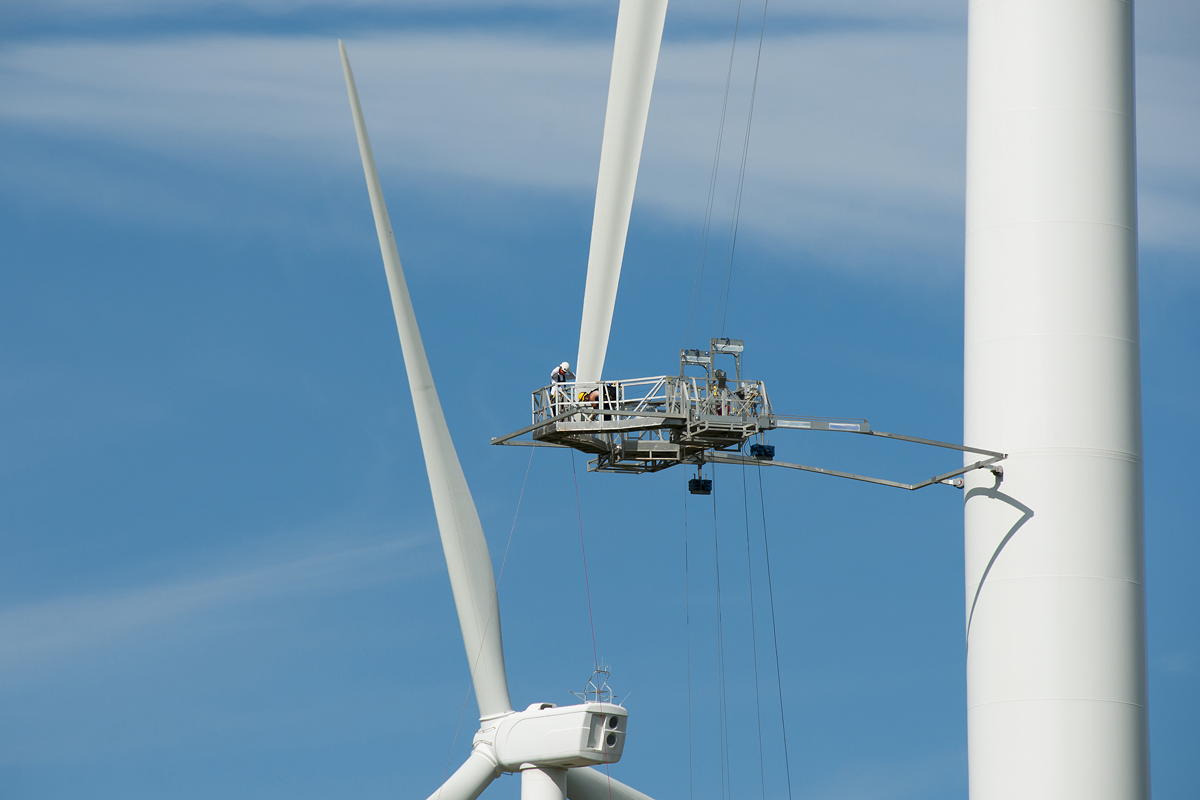
A. Technical management
The individual services in the technical management by Max Renewables include
Ongoing monitoring
- First and foremost the monitoring and control of all service and maintenance work. This is achieved by a remote monitoring system
all processes at the plants are permanently monitored. The resulting production data and other relevant data (e.g. wind speeds, weather, status of plant components, etc.) are read into a database and then analysed by a team. From a multitude of data, those of particular relevance to the wind farm owner are filtered and interpreted. - Faults are immediately diagnosed and rectified.
Extended continuous monitoring - Condition Monitoring
Current strategies for the operational management of wind turbines include extended parameters for the continuous condition monitoring of a wind farm (so-called condition monitoring).
The extended parameters can be obtained from the following sources:
- Vibration analysis
- Oil Analysis
- Infrared thermography
- Ultrasound
In vibration analysis, embedded strain gauges are also used on blades, gondolas and other heavily stressed parts to measure changes in the dynamics of the components. These can help to make an informed decision as to whether a component needs to be replaced prematurely.
From the data obtained, trends in the change of state of the individual components can be derived and predictions of faults can be made.
The extended continuous monitoring requires the increased use of sensor technology and results in an increased effort in data analysis.
Many errors detected at an early stage can be eliminated quickly and easily. This reduces the number of larger deployments, resulting in high cumulative cost savings. Larger deployments mean lead times (downtime), transport, crane fees and costs for components (component replacement) as well as labour costs. If larger deployments are minimized, this leads to considerable cost savings and improved system availability.
Insurers often grant discounts if the use of condition monitoring is proven by the operating company.
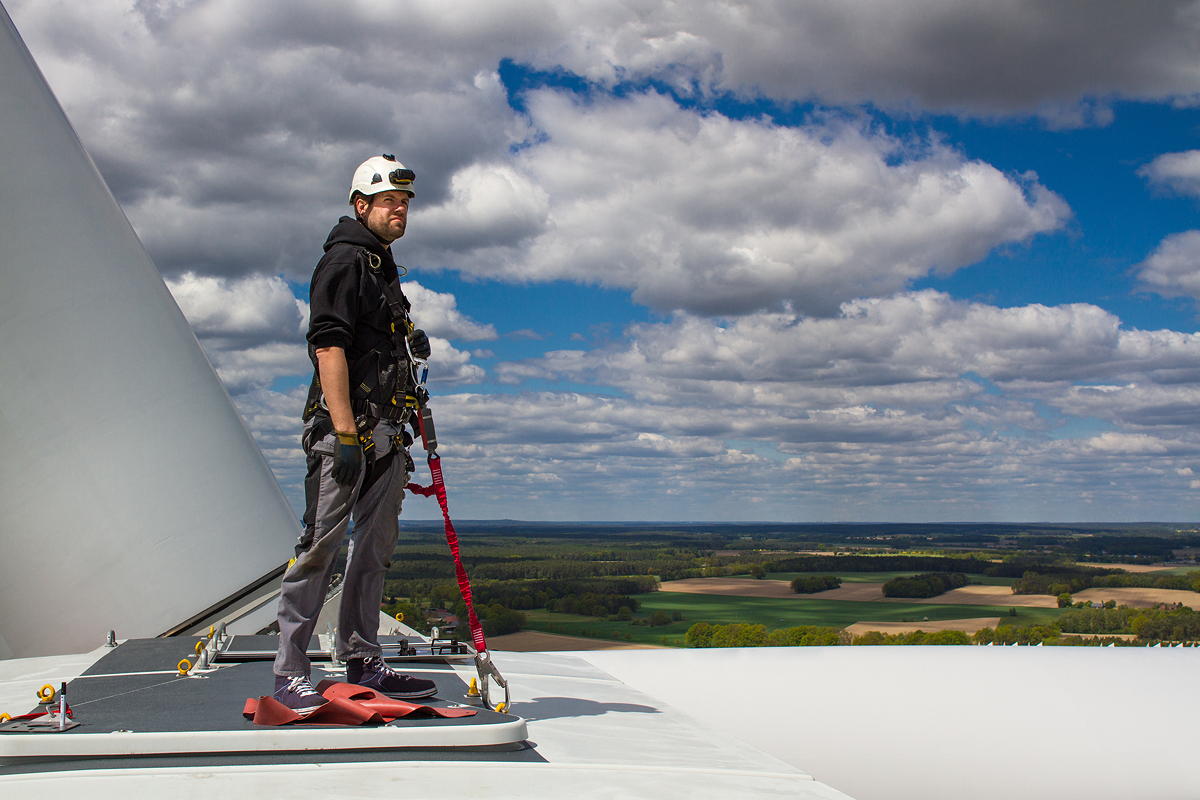
Inspections
A wind farm is inspected regularly. This usually takes place every three months.
Experienced technicians are deployed for this purpose.
- All necessary inspections and tests, e.g. safety checks, are planned and carefully carried out on a regular basis.
- Coordination of the maintenance of the transformer stations, substations and line routes.
-General inspections are carried out during commissioning and at the end of the warranty period with expert assistance and special documentation.
Scheduled maintenance and repair
In addition to regular inspections, scheduled maintenance must also be carried out and failed components must be replaced immediately if they are relevant to safety or operation.
To keep production downtime low, scheduled maintenance should be carried out in low wind periods; unforeseen repairs must be carried out quickly to keep downtime to a minimum.
Experience shows, however, that most turbine failures occur during periods of strong wind.
In a strong wind period, a one percent loss of availability can mean a significantly higher loss of power generation - therefore it is essential to organize and supervise important work carefully.
Keeping important spare parts in stock at the site can be an advantage due to the lead time in the procurement of spare parts.
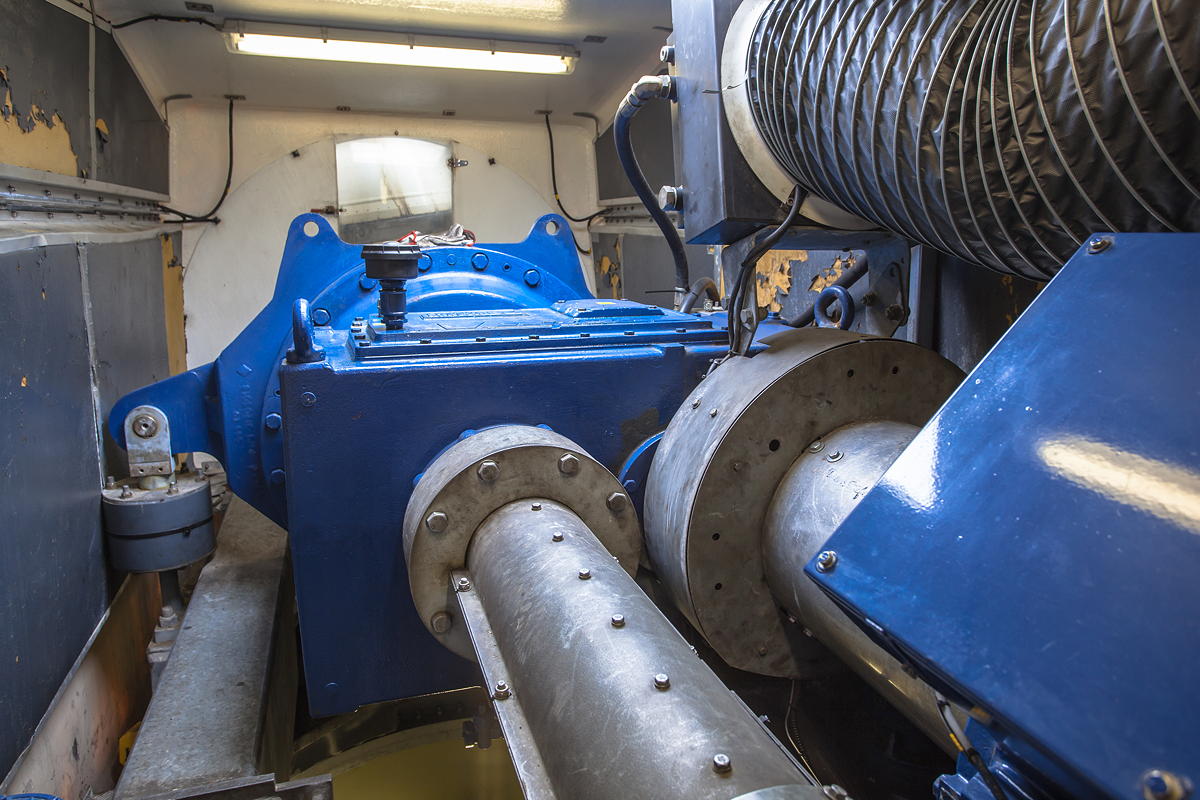
Other services Maintenance
- Regular communication with the electricians on site and the specialists of the responsible power supplier.
-Performing any necessary medium-voltage switching operations. - Coordination of maintenance measures/ winter service of outdoor facilities (maintenance of paths and crane parking areas).
- Reporting system: We prepare monthly and annual operational management reports on technical management, machine logbooks and life cycle lists of important components.
- Communication with landowners/leaseholders
Communication with authorities or energy suppliers. - Renewal investments/spare parts after termination of warranty or maintenance contract: Request for quotations, plausibility check and cost comparison.
Alarm
The technical management guarantees
24-hour alert. Depending on the alarm situation, either a local or remote restart is required, or technicians on site diagnose the alarm and rectify the fault.
We react extremely quickly in case of problems at the site. These include strong weather phenomena (e.g. flooding), intrusion of unauthorized persons, damage caused by vandalism or accidents.
B. Commercial management
Reporting system
Reports on the management and performance data of the park are provided monthly and annually. It includes a comparison of electrical power (in MWh), income, expenditure and budget, inspections, planned and unplanned maintenance, availability, power factors, alarm triggers and special events that caused downtime.
**
- increase in revenue**
Commercial management includes the economic control of the business.
On the one hand there is the optimization of the sales proceeds. I
The more MWh we produce, the higher the revenues. We cannot influence the wind, but we can influence the availability of the wind farm. Manufacturers usually offer a 97% availability guarantee during the warranty period.
A well-managed wind farm can reach power levels of 97 to 99%. In this case, all technological components have been excellently selected and the operations management manager will have a close relationship with his wind farm; he will know all important data by heart and provide analyses that go far beyond remote monitoring and a large remote-monitored and database-controlled operations management.
For larger wind farms (from 100 MW), each percentage point of availability can mean a value of several hundred thousand euros in additional revenue per year. We hear of a trend towards performance-based operation management contracts. Here, the additional revenue generated by the increased availability is usually shared between the park owner and the operator.
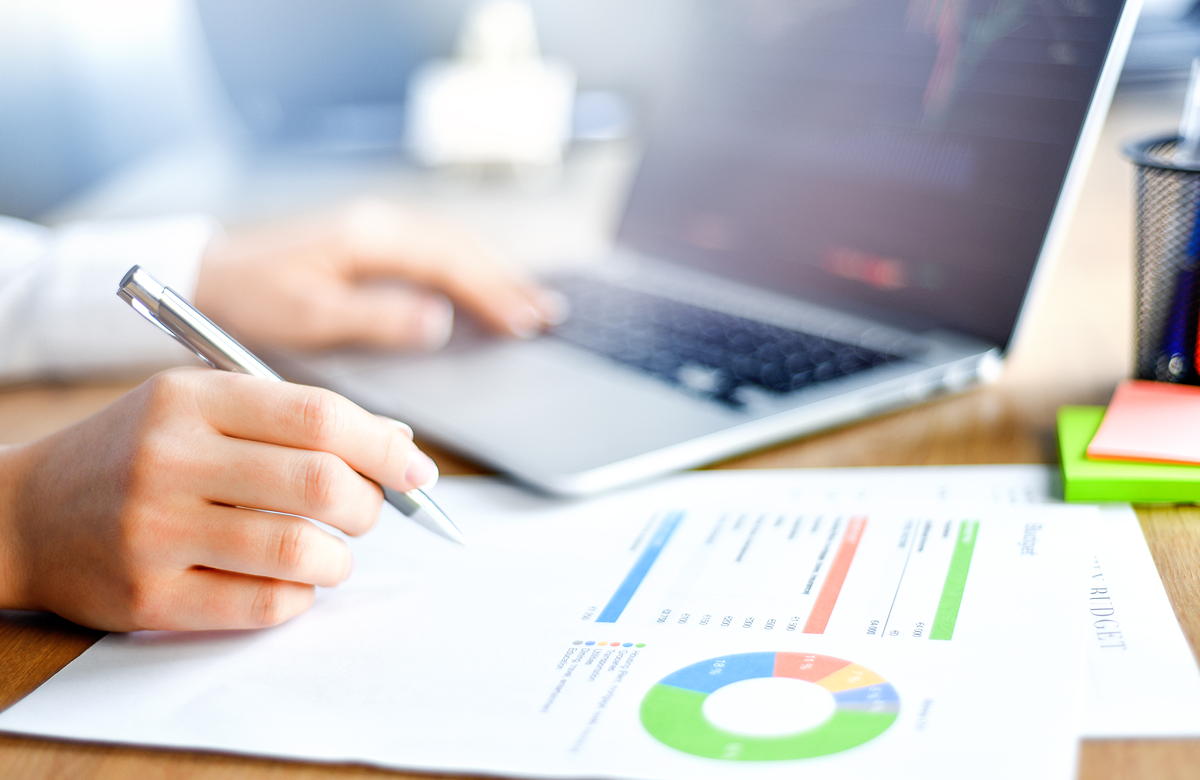
2. optimisation of the cost side
The local costs of the management (park maintenance, terrain maintenance, winter services, road maintenance, etc ) and the running costs such as insurance, own power consumption and administration are manageable. The leases for the landowners are fixed for 30 years and are inviolable.
The biggest cost blocks of the wind farm are the maintenance and repair costs as well as financing costs. The latter are controlled by the investor. The commercial management of the wind farm focuses on the optimization of maintenance and repair costs.
The first years of operation are subject to the warranty period, here only the labour costs of maintenance have to be paid. However, the calculation of a wind farm covers 15-20 years; the invested capital flows back in about 9 to 13 years, depending on the wind location and the respective project costs.
The supposedly highest level of safety is provided by fully integrated maintenance concepts offered by many wind turbine manufacturers. These must be paid according to the yield.
This relieves the owner of risk, but at a high price. As with all other insurances, a considerable premium is paid on top of the actual costs, so that the risk can be calculated exactly.
In the course of a full maintenance insurance, evenly high sums are paid throughout the entire period; however, the replacement of important cost-intensive parts (gearboxes, rotor blades, etc.) is increasingly necessary from the 10th year of operation. In the period before that, the wind turbine manufacturer only collects the money that he has to keep ready for later expenses.
We have often been told by banks that wind turbine manufacturers also represent an economic risk. If the manufacturer collects the maintenance money for 10 years and then gets into economic difficulties in the 11th year, this would be a catastrophe for a park operator, as he has paid high fees for years but would have to pay for the services in the years 12-18, which are very expensive to repair.
As a conclusion, it can be concluded that even with a good knowledge of the system, reserves can be built up to make long-term maintenance more cost-effective than in full maintenance concepts.